Every construction project is vulnerable to radiation, noise, temperature, and barometric pressure hazards. Without preventive safety measures, your construction workers might face risks like falling, tripping, and slipping. Aside from that, they might inhale dangerous materials like lead, chromium, and asbestos that might cause health issues like lung cancer and asthma.
To avoid these costly work-related accidents, you have to adhere to the requirements administered by the occupational safety and health act (OSHA). Once you do so, you will be able to follow the timeline of your projects and protect your workers from life-threatening injuries.
This article provides you with eight economical ways to improve construction site safety.
1. Run Regular Facility Inspection
Routinary construction site inspections are vital because they ensure that operational activities follow standards and requirements. During this process, you can inspect the accuracy of paints and coatings, track worker schedules, and review drawings to discover errors. This strategy will help you develop a high-quality building with all the proper measurements without sacrificing your budget.
When carrying out inspections in your construction, you need to schedule them during commencement, excavation, and foundations. Before the project, you must survey the property’s condition to check the fabric structures for construction projects and planning permissions. After that, you must conduct thorough site walkthroughs to assess whether everything is completed and ready for intended operations or occupancy.
2. Organize Training For Construction Workers
Construction machinery is crucial in speeding up processes like crushing granite, mixing concrete, and getting rid of heavy trash. If an under-skilled worker decides to use it, they might cause bad equipment-related accidents like running over a colleague. Alternatively, they might unconsciously open containers with harmful emissions like chemical by-products or loud noise.
To prevent these situations, you have to organize training for your construction workers that will help you impart knowledge and skills on proper material handling. This program should have policies on the correct physical structure when lifting devices and how to properly operate moving equipment like conveyors and loaders.
3. Implement Site Cleanliness
Regularly cleaning your construction site is vital to eliminate wasted materials and keep it free from dangerous bacteria. Instead of navigating through scattered debris, your workers can move freely and attend to their tasks. When business partners decide to pay a visit, you won’t have to gather your cleaning staff to clean the place, and they will continue to support your projects.
When keeping your construction site clean, you must provide trash bins in multiple areas to motivate your workers to pick up trash along the way. Next, you have to install portable lavatories behind construction barriers so the public won’t be able to access them. Then, you have to implement toilet facilities so your staff and authorized visitors can implement proper hygiene.
Aside from that, you must protect your construction workers from harmful dust-related illnesses, especially during the demolition process of older buildings. For instance, you may invest in safety ventilation masks for all your staff on your site. Doing so will help you control dust and prevent airborne pollutants.
4. Limit Access To Restricted Areas
The restricted areas in construction sites may produce loud noises, have heavy moving equipment, and are prone to collapses. When workers are operating in these locations, they are less likely to focus on outsiders who are navigating through them. If your guests are not careful, they might face falling objects, inhale airborne dust, and develop long-term hearing issues.
To avoid this incident, you must limit access to these restricted areas so your construction workers can concentrate on their tasks. For instance, you may add barriers on entryways, temporary fence panels and install surveillance cameras to help you monitor intruders. In addition, you should include an emergency contact number and directors to the site office so that all safety measures are readily accessible.
5. Adopt Safe Eating Protocols
Your construction workers are expected to eat on-site during projects so they won’t have to go outside and waste time waiting for orders. However, they might bring food to the area without proper storage, which leaves it open for contamination. If chemicals spill on it, your staff might suffer from food poisoning or even fatalities in most cases.
To protect your construction staff from these incidents, you should design a room where they can eat their packed food. Before entering this area, you must provide them with sanitization tools as well as a hand wash sink to ensure that they eat without debris and clean their hands. If you have the budget, you should consider investing in a fridge where they can store their food. Then, you may also add a microwave oven so they can reheat their meals.
6. Provide PPE
Accidents, such as slippery wet floors or loose falling debris, are common on construction sites. Therefore, you have to provide your workers with durable personal protective equipment (PPE), so you can protect your staff from the safety and health threats on the job. As a result, you can minimize their exposure to hazards like gases and dust.
So, here’s a list of construction PPE that you have to look for:
- Hard Hats: This equipment is commonly used by construction workers operating in areas with a potential threat to the head, like falling objects. For instance, this protective clothing will protect them against accidental head contact with exposed electrical conductors.
- Protective Gloves: This equipment has special back padding that reduces the effect of objects falling or touching their hands. For example, this clothing allows your staff to handle hazardous materials, corrosive chemicals, sharp objects, or items with hot or cold temperatures.
- Hearing Protectors: Since construction sites can expose your workers to noisy sounds, this equipment will protect them from severe hearing damage. These products may include earplugs and ear muffs that can reduce the noise levels from reaching their ears. Aside from that, you also have to sponsor employee hearing tests so you can spot signs of hearing loss and prevent auditory accidents.
- Face Shields: The purpose of this equipment is to protect your staff’s entire face from hazards like chemical splashes and flying objects. In addition, they can prevent themselves from touching their nose, mouth, and eyes to protect themselves from contaminated droplets.
- Fall Protection Equipment: Most of your construction workers will operate above the establishment, which puts them at risk of severe falls from slipping. Therefore, you have to provide them with this equipment so they can avoid getting life-threatening injuries or dying in the process. These devices may include safety net systems, covers, and guardrails.
7. Replace Broken Equipment
While this strategy may sound expensive, replacing low-performing equipment could be the best investment in your construction site. These advantages may include avoiding machinery-related accidents, improving the quality of work, and boosting brand value. Aside from that, you won’t have to frequently pay for repair costs since most of the latest technologies require less maintenance.
Before investing in new equipment, you have to properly dispose of old machinery because you might be able to sell functional parts. Instead of throwing it in a landfill, you should consider auctioning high-demand technologies so you can sell them to a large group of interested buyers. Alternatively, you could trade it for the latest models so you won’t have to worry about selling them because the manufacturers will take care of the logistics.
Once you get rid of your old equipment, you must carefully consider several factors as you buy new construction machinery. For instance, you have to check the manufacturer’s credibility because your equipment must withstand unpredictable weather conditions. Additionally, you must know if it is fuel efficient so you can save a lot of money in the long term without sacrificing its features.
8. Automate Communication
Effective communication is key to completing your projects and improving construction site efficiency. When you invest in it, your supervisors and workers can collaborate, allowing you to meet schedules ahead of time. On the other hand, poor communication leads to directing the wrong information to the incorrect person, which can lead to workplace accidents.
To avoid project delays and protect your construction workers, you must improve communication within your site. With that, you must use a construction management platform to enable your team to stay on track with deadlines, so everybody knows their responsibilities and safety measures. Furthermore, your staff can quickly receive real-time responses from your supervisors to accept their requests, so they won’t have to wait hours to get their permission.
Aside from this software, you need to provide your workers with other handheld or wearable devices so you can communicate with them without relying on the internet. For instance, you may give them smartwatches, headsets, and walkie-talkies so they can still send updates during the operations. This equipment is helpful during roll calls or emergencies where there’s no signal so that you can send your emergency response team immediately.
Key Takeaway
As a project owner, you need to give your workers the resources to fulfill their jobs effectively without sacrificing their health. Therefore, you should consider following these eight economical ways to improve construction site safety. Once you do so, you will comply with OSHA while creating a safe working environment for your staff and visitors to keep your projects moving.
Related Posts
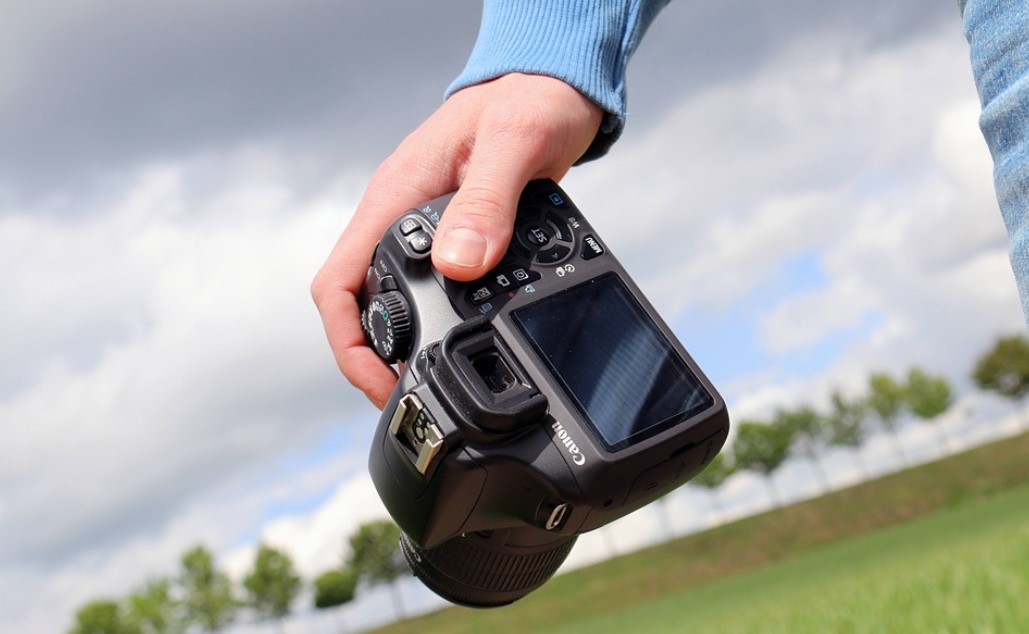