Metal Injection Molding is a useful metalwork technology to produce small but complex metallic parts in high volumes. From this blog, you will run the ins and outs of injection molding aluminum and other services. Then, you make the best decision on the 3D metallic prototype or final product you want. This entire blog is highly advisable to be read before beginning the mass manufacturing of these metallic parts.
A Quite Simple Concept But With A Complex Process
Ceramic Components first developed this idea to plastify powdered raw materials. This was the task performed using thermoplastic additives. Further, the injection molding method came into the picture to form complex components.
In the 1970s, Raymond Wiech from the USA introduced the use of metallic powders into this method. He is also widely called the inventor of Metallic Injection Moulding.
The process of injection molding aluminum or various other metal powders:
-
Preparation of the feedstock
The raw material for this process is the metal powder and the thermoplastic glue or binder. Though, the thermostat additive must be removed from the final product after the injection molding is complete.
The properties of the metallic powder will define the finishing and final properties of the Metal Injection Molded material.
The blended mix will be plastified at a higher level by using an extruder or a kneader.
This intermediate product is termed the feedstock. The feedstock is often available at multiple stores or factories. This can be purchased from there when you have ready-to-use machinery for processes like injection molding aluminum.
-
Injection molding brief
The parts of the bigger tool formed through the MIM process are similar to the real-life plastic parts. These parts’ size made through the Injection Molding method must be equivalent to the plastic component when produced without this method.
-
Removing of the binder
You have to get to this step removing the binder after the injection molding of the parts. Through this step, you obtain parts of the interconnected pore network without having to mess with the component’s original shape.
After the removal of the binder, there might be some part of the binder still left. It holds the various metal powder particles together.
However, not to worry. The pore network is powerful enough to evaporate the same with the conception of the sintering. This usually happens when the sintering necks will take place between the left-behind metallic powder particles.
-
Sintering
Through this step, you eliminate most of the metallic powder particles that were earlier occupied by the binder. The implications are such that the MIM parts start to shrink.
The shrinkage percentage ranges from 10 to 20 percent during the sintering process. At this stage, you can eliminate the use of those shrunken parts.
Otherwise, you can process them further using the usual metalworking methods. These treatments on the residual of the MIM particles trapped by the binder would be either heat or surface treatments.
These treatments work on these particles in the same as on the cast or wrought parts.
During certain medical, automotive, and aerospace applications of this final step, HIP or Hot Isostatic Pressing method comes to the picture.
It is successful and better to remove the remaining porosity in the above categories for manufacturing tools or parts.
Designing of Metal Injection Molding (MIM)
Today, as the technology grows exponentially, MIM is available for manufacturing various structural materials. These can be for industries like military, medical, electronic, aerospace, and hardware.
The metallic powder has to be less than 25 microns in size for starters. It must be sintered to a higher density as the last step in the process. Though, the particles must not bring any change to the chemistry of the alloy chosen for manufacture.
If the powdered particles have these properties, then MIM is the best method to complete the required materials’ manufacturing.
Often, MIM is quite an attractive method to fabricate soft magnetic and metallic materials. It further provides a net shape component found in the annealed condition.
This condition is required for the best possible magnetic response.
Metal Injection Molding is also a viable method to produce copper materials. Copper shows the required amount of electrical and thermal conductivity. So, MIM copper can be best for thermal management applications or electrical connectors.
Related Posts
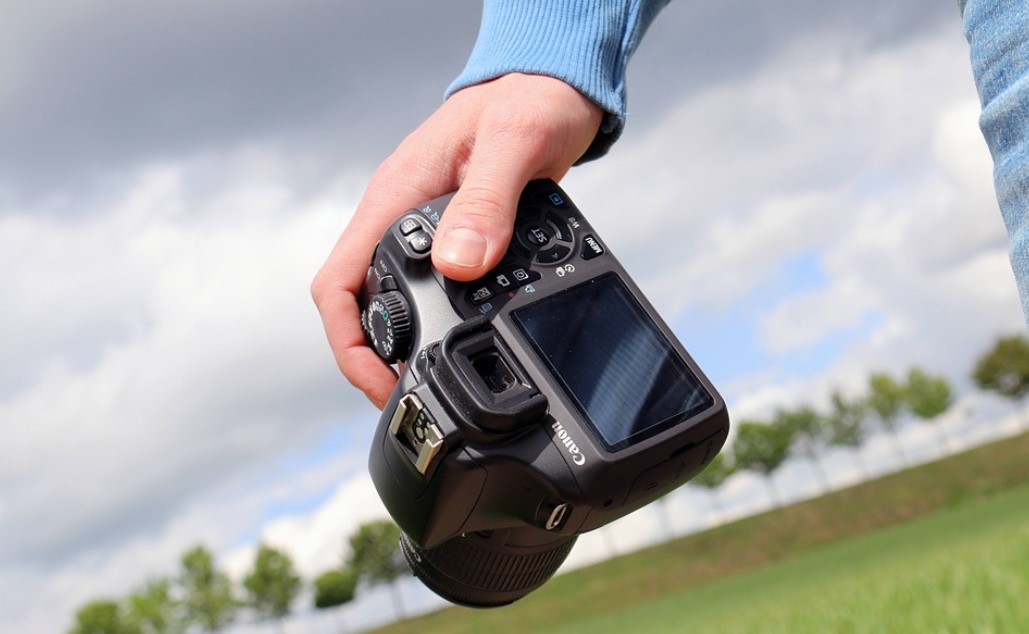