If you are an engineer, a flange spreader would be a handy tool in your arsenal. The flange spreading tools are for industrial engineering and construction projects in general. They are already available in various ranges of their configuration as per the demand of the ongoing project.
There are multiple uses like separation of pipe joints where an engineer uses the spreaders.
Before knowing how they work, let’s get into basic information about mechanical flange spreaders and their tools.
Types of spreaders:
There are 3 common flange spreaders:
- Wedge type
These are available with a hydraulic cylinder. Otherwise, they use a mechanically operated system.
- Expanding collets
They are used mechanically only. There is no involvement of hydraulic cylinders.
- Mini-gap flange
They use a wedge with a fixed size. These, too, are used mechanically in the engineering/constructing project by an on-site engineer.
Flange tools or type selection method for newcomers:
You need to first know the dimension of your flange. For that, you can use any online tool for a guide. The dimension can include the flange specification, class or pressure, and its diameter.
These tools help in deciding the flange spreader type to use for the flange in the upcoming engineering project. Otherwise, if you have a project manager, they will help you with the same.
Using a wedge flange:
Ensure the wedge flange tool kit you use is not defective. Also, inspect its hydraulic cylinder or another component. They must work properly to avoid further complications during flange spreading.
Now, connect all the couplers from the tool kit available to you. Do not start pressuring the hydraulic cylinder before that. You need all the couplers in line and connected to do that.
Then, to insert the spreader, first place two flange bolts at a fixed location with loosened nuts. Then attach the flange inside easily later on. By doing so, you can avoid any friction or unwanted delay when you want to use the flange spreader. This tactic also prevents the dropping of existing gaskets.
- Determine the most possible and feasible position of the tools around the joints. At least 2 wedge flange spreaders must be put in use.
- When you know which flange spreader to use, place it in the access gap. The width of the selected gap must be brimmed up to the heel.
- Actuate the tool to spread the flanges.
- As the joints are apart till the desired distance, use the safety blocks there.
- Check whether the safety block’s full width is in use before retracting the tool until the entire flange gets applied to those blocks.
Using an expanding collet flange:
When there is no access gap between the selected flanges, then the expanding collet flange is the perfect solution. This flange uses two flange bolt holes to secure the spreader in the desired position.
- Measure bolt size before deciding the size of the collet. The undersized collet goes through the hole, and the oversized collet will get it jammed. You don’t want that. So, measure the size of the bolt and the collet properly.
- Insert the collet into the selected tools.
- Two tool halves get inserted into bolt holes then.
- Double-check that the collet is attached to one flange only.
- When the collet is properly engaged, it can be tightened further.
- Lock the cantilever and actuator in this position.
- After the actuator receives tension, use a torque wrench.
- Finally, the flanges separate. Then, you use the safety blocks in the right place.
Using a mini-gap spreader:
You use a mini-gap flange spreader on smaller flange joints with lower pressure. There has to be a minimum access gap of about 2.00mm.
- Know the size and class of the flange you wish to separate.
- Use two spreaders at a 180-degree distance on the flange joint.
- Spreading bars will only fit the desired flange specification. No two bars are meant to fit the same hole. Keep that in mind while using them.
- Place your mini-gap tool over the joint and align/attach it further with the stud hole.
- You engage the bar with the help of the tool’s leg and the stud hole of the flange.
- Ensure that the bar is fitted properly even through the tool’s second leg.
- The wedge must be fitted between the gap that the flange faces. Double-check this point.
- Turn each tool half a turn until you reach the gap you need in the flanges. But ensure that you apply the force pretty evenly.
Related Posts
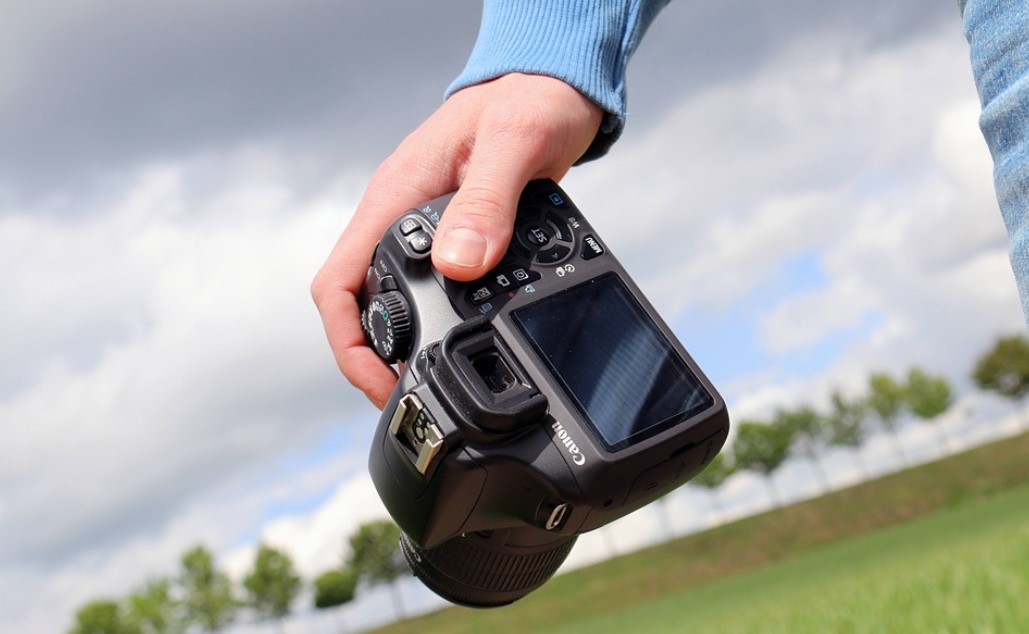