The healthcare industry continues to evolve, increasing longevity and quality of life. Advanced clinics use the latest technologies and innovative medical devices to provide prompt and efficient healthcare services. While medical equipment gets smarter, more secure and increasingly fault-tolerant, it is still prone to errors that can cause irreversible damage to patients’ health.
The imperfections of today’s medical hardware and software emphasize the need for thorough testing and quality assurance. Tough standards and regulations have been adopted on local and international levels. Prior to releasing new healthcare products, manufacturers need to comply with generally accepted standards for both product quality and the manufacturing process.
Why Respect for Standards is Vital
New standards emerge as a consequence of grave errors. Regulatory bodies establish strict frameworks to prevent problems that others have already faced and paid for. Respect for generally accepted standards is vital to preventing device malfunction and protecting human lives.
Regulations have become stricter than ever before in recent years. Healthcare devices are increasingly powerful and complex. They automate many routine tasks previously performed by medical staff and enhance the accuracy of diagnosis and treatment. While this is a positive trend in general, the complexity of medical equipment makes it more vulnerable, unstable and less manageable.
It is easier to gauge the quality of simple tools like a scalpel or a needle than to determine whether intricate systems underpinned by the latest software function adequately. Automating and digitizing medical services enables healthcare organizations to enhance their overall performance, but by shifting responsibility to machines, they have limited control over certain processes. Very few physicians understand the operating principles of cutting-edge apps and devices, or what actions to take to prevent harm to patients’ health if they fail.
To ensure absolute fault-tolerance and safety, testing must become more complex, sophisticated and laborious. As a device manufacturer, you need to pay as much attention to quality assurance as you do to the design and implementation of innovative solutions.
Compliance with universally accepted standards throughout the entire process of product development and distribution will help you avoid complaints and lawsuits that can ruin your reputation. Testing will help you pinpoint bottlenecks, fix mistakes and prevent harm to patients.
Development of a Testing Strategy
QA considerations should be paramount at all stages of product development, launch and supply. Delaying testing to the end phases of product development can be costly if you have to backtrack to fix bugs and deficiencies. It is better to test as you go, to reveal and correct minor mistakes along the way.
Your testing team should be involved in the project from day one, to determine quality requirements based on the device’s specific purpose, components and intricacies of the manufacturing process. Those requirements will determine the types of testing to be done, the choice of technologies and tools, and the environment in which they will be applied. They will also dictate how the development team responds to different situations, limitations and constraints.
The coordinated work of multiple teams in project development and testing at every stage ensures high productivity and prevents quality issues at the product release phase. You should assess each process individually, to simplify the search for mistakes and their correction.
Structure of a Testing Strategy
Tests performed throughout the project correspond to the design, development, and launch stages, and to the intermediate steps within those stages. Each link in the testing chain should be geared to the general goals of the quality assurance strategy, and evaluated individually as a separate process.
Once a certain step is completed, the results are tested for compliance with requirements established at the planning stage, using a specific set of procedures and metrics. If mistakes are found, work on the project stalls until they are fixed and Improvements are implemented.
Microprocessor Testing
Microprocessor testing is at the core of the QA process for most medical devices. A testing team must:
- make sure all transistors are connected and electronic signals are effectively transmitted
- test the microprocessor chip prior to its installation in a circuit board
- gauge logic gate functions of integrated circuits
- connect all elements to a circuit board and test mounting to detect defects of assembly, extra and missing components, open connections, etc.
The testing team can use special equipment to access the tiniest structural parts without affecting their smooth operation. They can run a quick analysis, measure all features and make accurate decisions about any necessary changes. It is important to view each component as both an independent entity and as part of the entire system, interconnected with other components that can affect its operation.
Compatibility Testing
Testing during manufacturing is insufficient to determine whether a product can cope with the tasks and loads demanded in the field. Today’s healthcare organizations use a large number of devices produced by various brands. When supplying a solution to a healthcare facility, you are obligated to ensure its seamless integration into any existing systems. It should be able to adequately transmit and receive data to and from other devices, and withstand internal errors and the failure of other units in the chain.
The healthcare industry has a low tolerance for faulty equipment, since human life is at stake and failures are costly. Technology can empower healthcare services, but only if used with caution. Leverage the best QA practices to create high quality equipment that changes the world of medicine for the better.
Related Posts
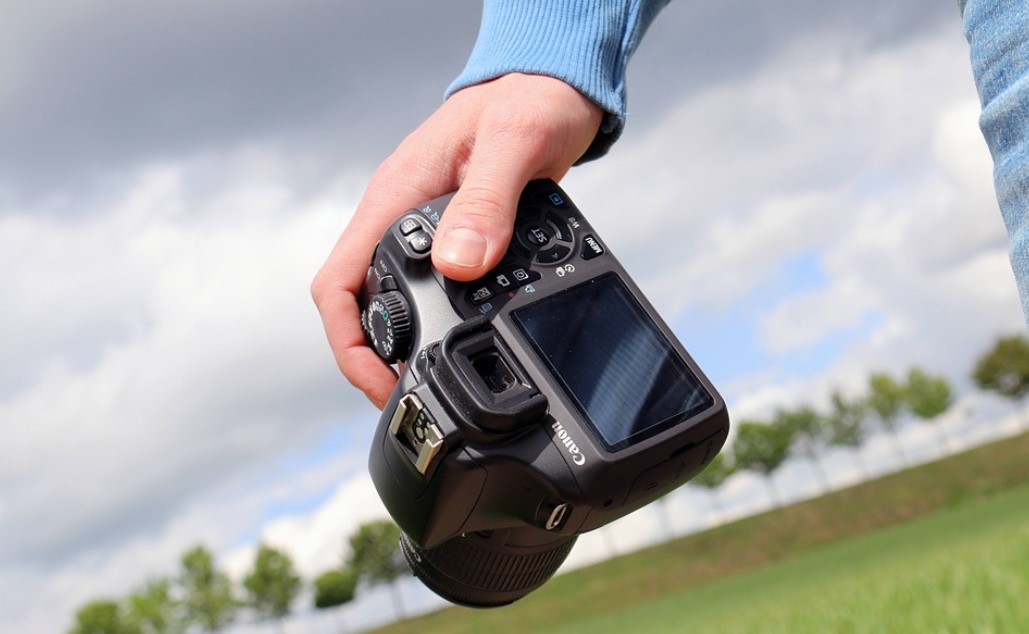