The process of how plywood is made is extremely interesting, and in this article, we will go through it step by step. Let’s get started!
Step 1: Felling
Trees are the backbone of plywood materials. This shouldn’t surprise you, as wood is what plywood is made of! After a few trees are cut down and their branches chopped off, they are taken to a mill, where the real work of making plywood begins.
Step 2: Preparation
The next phase of plywood production involves removing the bark from the wood. The logs are sent through saws that tear away the bark completely. After the logs are stripped of their bark, they are taken to a mill to get chopped up. Here, the wood takes the form of the long sheets that we all know and love! They’re called peeler blocks.
Step 3: The Veneer
These peeler blocks then go on an adventure of their own! Before the veneer can be applied to the wood, it is usually softened by being heated and then soaked. Now, how long it takes is usually dependent on the wood type and dimensions, but it’s usually somewhere between 12-40 hours, give or take a few.
Veneer sheets are often stored in trays or rolled and then cut as per requirements when the time comes. However, a laser is used to scan for abrasions to ensure that the veneer is of good quality. Once it goes through, the veneer is applied to the plywood using a hot press.
After that, every sorted sheet is dried. This is because if they are left by themselves, they will absorb moisture and shrink in size. This makes bonding impossible, which is bad. Mechanical dryers are often used to get this done.
The veneer is graded as it exits the dryer. In the parts of the boards where the look doesn’t really matter, for example, the interior layers of plywood, the veneer is applied using tape or glue.
Step 4: Finish
After the veneers come the finishing touches. During this process, sheets go through a press and get squeezed tight with others. They’re exposed to high temperatures and pressures, causing them to stick together as if their lives depended on it. This ensures that the glue is applied correctly and that it is strong enough to weather the stresses of daily life.
After this, the sheets are sized and sanded down for use. This process requires precision, and though extreme caution is used, mistakes do happen. That is why there is always a final examination of quality, after which repairs are made.
After all this is done, the plywood that gets selected for shipping is given a trademark. This lets buyers know all the relevant information about the wood, like the mill where it was made, how it fares against exposure and other facts. These boards make it to the warehouses and then our homes!
Conclusion
Now you know how plywood is manufactured! As a rule of thumb, only around three-quarters of a tree can be made into plywood, which is pretty wasteful. However, several new processes of how to make plywood are in the works to boost this number and make plywood production even better! Nordecoply manufactures quality plywood in bulk with delivery throughout India.
Related Posts
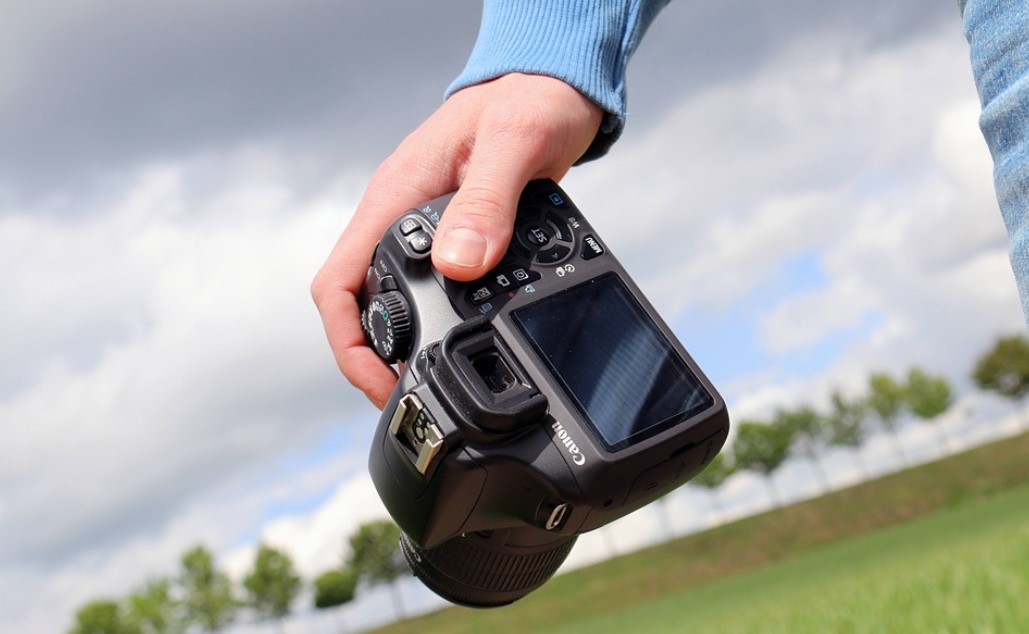