Motors are widely used in industrial applications. As motor technology becomes more complicated, motors technicians must understand the causes of motor failure. The problem is that the causes of motor failure are complex and nuanced, as various mistakes can cause problems that eventually lead to motor failure. Electric motors are ubiquitous in the industrial environment, they are becoming more sophisticated and technical, and sometimes maintaining their best performance is difficult. It is important to remember that the causes of motors and driving problems are not limited to a single area (mechanical and electrical problems can cause motor malfunction), and the availability of correct information can mean the difference between high idle and walking assets.
The two most common problems that can cause motor failures in the industry are weakening of ending insulations and the worn bearing; thus, the electric motor repair is very costly and hectic to the task to deal with. While, these conditions can be caused by the variety of factors, which are as follows;
Power Quality Problems
Issues which affect the motor’s energy quality are usually caused by voltage imbalance, transient voltage and harmonic distortion.
Transient Voltage
Along with the system of distribution of the industrial plant, the transient voltage case may arise from various external and internal issues. Similarly, the two commons reason includes
- When the power of neighbouring machines off or on.
- Condition of the environment is due to the outside weather condition.
Unbalance Voltage
Single-phase load is usually in a three-phase power distribution system. If the resistance is passive or the load distribution is unbalanced, the three-phase distribution is unbalanced. The three most likely causes of voltage imbalances are:
- Problems with cable of motors
- Termination of motors ends
- Issues with winding components
In a three-phase power system, voltage imbalances cause stress at all three levels.
When imbalance happened, an excessive current at both levels (and probably two or three levels) causes an increase in working temperature, which consumes at insulation. It is, therefore, important that each phase has the same voltage level. A three-phase power analyzer can detect causes of voltage imbalances.
Harmonic Disorder
This phenomenon is called harmonic distortion when excessive wind currents affect engine winds. In this case, excess energy flowing is useless to rotate the motor shaft. What harmonic does is flow through a spiral device and use excess energy. Over time, harmonic distortion can cause heat to build up, affecting the insulation of the winding components.
Frequency of variable driver Problems:
If the motor displays signs of malfunction in a particular area, the problem usually depends on the output sigma current, reflection or overcharge current on the output drive.
Reflection on the Drive output signals of PWM
To control the voltage transmitted to the motor, use a frequency control called pulse breed modulation (PWM). If load and source impedance is unbalanced, the reflection will occur. The impedance mismatch would be liable to increase because of the following reasons.
- Poor installation
- Mismatched of incompatible Components
- Use or worn equipment
Of course, the reflection height can be as high as the DC bus voltage in the motor drive circuit. Eventually, the corrosion insulation inside the winding of motor can lead to unpredictable and frequently costly working hours. Such problems are very serious and should be examined and analyzed using the four channels of the oscilloscope.
Mechanical problems:
If the problem is due to mechanical failure, it is usually caused by uneven, worn or loose or unbalanced shafts.
Misalignment
If the drive shaft of the engine or motor is not correctly aligned with load, “misalignment” may occur. Otherwise, problems may occur if the machine accessories are not in the correct order. While flexible connections or couplings can add the wrong settings, it protects the entire connection itself.
Despite the flexible connection, adjusting the shafts can cause troublesome regular shaft shocks. When this happens, mechanical overload rises and motor become overloaded. Besides, the inverter increases engine load and vibration magnitude. Misalignment can be divided into three types:
- Angle row misalignment: The shaft’s counter lines are not parallel and intersect.
- Composite misalignment: an arrangement of angles and parallel distortion problems.
- Parallel distribution: The centerline axis of the shaft run non-concentrically dissimilar.
In some cases, the wrong alignment is a mixture of parallel and angular issues. However, this problem is generally regarded as a misalignment, as it is usually easier to solve each problem.
The overall impact of the wrong alignment on industrial engines is very serious as they can cause severe wear on the mechanical parts. Similarly, this leads to initial failure, and also misalignment is a serious problem and can be detected by a laser channel corrector.
Installation Problems:
Occasionally, when a problem occurs, the motor may be caused by improper installation, which can cause pipe stains, soft feet or shaft voltage.
Therefore, troubleshooting motors are an important topic that has to be divided into several different categories.
1.Electrical overcharging
Overloading or the excess current causes are overheating in the motor winds, which is greater than the design current that the motor can safely and effectively carry. Low voltage may cause the motor to rotate at higher current to maintain torque. It may also be the result of a shorter conductor or excessive power supply.
Solution: Electrical overcharging can be avoided by installing an effective shield or the protection of over current that detects overcurrent and intrudes the power supply.
-
Low resistance
Low resistance is the most common cause of motor failure and is undoubtedly the most difficult to overcome. Low resistance is initiated by deteriorated wind insulation due to overheating, corrosion or physical damage. This can lead to insufficient insulation of wires or motor winds, which can cause leaks and short circuits, and eventually motor failure.
Solution: Check the insulation regularly for signs of wear and replace it first for low durability.
-
Overheating
About 55% of electrical motor insulation failures are due to overheating. Poor energy quality or high-temperature work environment can cause overheating. Each motor temperature increase of 10 ° C reduces insulation resistance by 50%.
Solution: It is important to keep the motor as cool as possible and to ensure that the working environment is as cool as possible to prevent malfunctions.
Final Words
The most common causes of motor failures are broken winding insulation and worn bearings, but these conditions can occur for many different reasons. However, each electric motor as estimated service life, typically between 30,000 – 40,000 hours. Depending on proper maintenance, however, they may break down faster. Understanding the five causes of motor failure and taking steps to reduce the risk of these failures will give your motor the best chance of maximizing life.
Related Posts
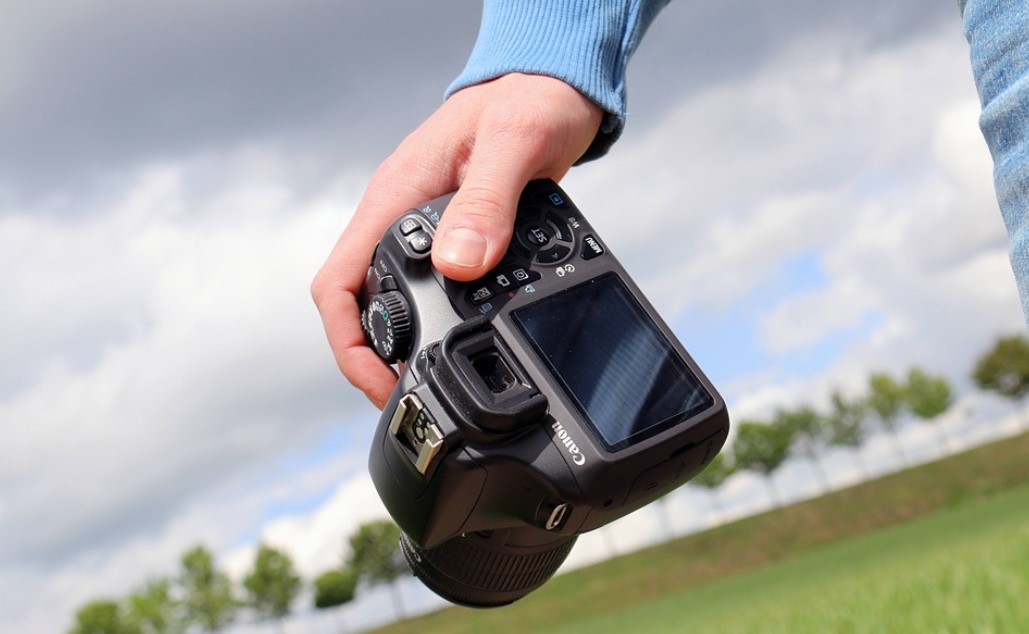