Lots of terms and technical names are used with industrial manufacturing that have become commonplace and as generic as xeroxing a document (which in reality is misusing a company’s name, Xerox). However, while many of the names are easy to remember, many folks don’t automatically know or remember what they actually reference. CNC machining is one of those terms. Put to the test, a lot of folks in manufacturing will know what CNC refers to in a process, but they won’t necessarily know how to define the actual term. Does it matter? In manufacturing knowing exactly what CNC machining provides makes a big difference in understanding the output that will be delivered, especially in custom fabrication.
Enter the Computers for Fabrication
Technically speaking, CNC machining refers to the use of computerized numerical control machines or CNC for short. These are fabrication equipment or finishing equipment that handle high production of material from raw state or unfinished state to a completed end product. The process of operation is managed and controlled by a computer instead of a human being actively being engaged in the operation. Some of the most common build equipment that uses CNC systems include lathes as well as mills, all of the movement being controlled by programmed instructions sent by a computer to exact details and specifications.
A Useful Standby Process Where Big Production Has Gaps
In application, CNC Machining fills the gap when a fabrication facility needs a small supply of parts of a unique shape or size, needs a replacement part, or wants to experiment with a prototype. The plan, dimensions, shape, and specifications are programmed into a computer with the requisite software, and then the code takes over with the instructions directing the fabrication machinery to produce the part. The CNC fabrication itself happens with very basic shape modification via drilling and milling while the position of the material is turned appropriately to allow the necessary change. While the process won’t build an assembly, it definitely can produce all the parts to do so efficiently and exactly. No surprise, every major fabrication shop has a CNC system on-site or contracted service to help with part needs that come up on a regular basis.
Elimination of an Otherwise Costly, Labor-Intensive Need
Industry-wide, CNC machining has filled the hole that otherwise would not be met or would create significant delays in manufacturing processes. The approach makes a lot of sense and practicality as well. The same work done to the specificity the computer can produce would be extremely hard, it would take far more than one or two operators to handle, and the cost would be far more in overall production. On-the-spot fabrication was one of the reasons why old factories would have so many different shops in the facility to fabricate products. However, that created ultra-specialization which, when someone was not available, also created work stoppages that became costly. Instead, when computers were married up with fabrication equipment in a straightforward input manner, the ability to custom-produce a part was immediately practical and useful. Aviation shops, for example, constantly need CNC-machined parts to replace old ones on planes that need to be taken off and swapped with a new ones to maintain flight safety.
Specialization in Support as a Career Path
The specialists who operate and manage CNC machinery find application in dozens of industries. Wherever there is a need to fabricate durable parts and components, CNC machining is typically applied. That includes tooling, automotive and aviation fabrication, tech hardware build, aerospace, medical equipment fabrication, and a lot more. There isn’t an industry today that has metal parts in its assembly process that doesn’t include some kind of CNC machining involvement somewhere in the process. The specialist is particularly important in developing the design files the computer will follow, installing them, testing, and running the operation to meet quality expectations. That involves a combination of technology and fabrication training unique to the management of a CNC system.
What to Expect Tomorrow
It is very likely that CNC machining will be the roots of full automated fabrication in the future that only Hollywood and science fiction writers play with now as a concept. The fundamentals are already proven; with enough coding and direction, machines are extremely specific, accurate, and reliable in production. A key advantage is the complete elimination of human error, an age-old problem in not achieving a high degree of accuracy quality needed for highly technical tools such as medical-surgical equipment.
There is no shortage of what CNC machining can be used for as well. Metals are what most people think of at first. However, CNC processes can be applied to wood, plastic, fiberglass, foam, and anything that can be drilled, milled, and ground. That makes for a wide assortment of applications and industry solutions, regardless of how the end product will be used. It has also been a godsend technology for the secondary market in many industries, providing avenues for business for many contractors and part suppliers who take care of niche needs that large manufacturers often have.
Not Being Replaced Anytime Soon by 3D
Some wonder if 3D fabrication will replace CNC machining soon. While there is definitely a place for 3D crafting, it’s almost all in prototyping. In the meantime, when it comes to durable production-ready applications, CNC machining remains the primary go-to source for manufacturing custom work. Evden Enterprises Inc has continued to be a long-standing source for professional CNC work and projects, especially under demanding timelines and production needs.
Related Posts
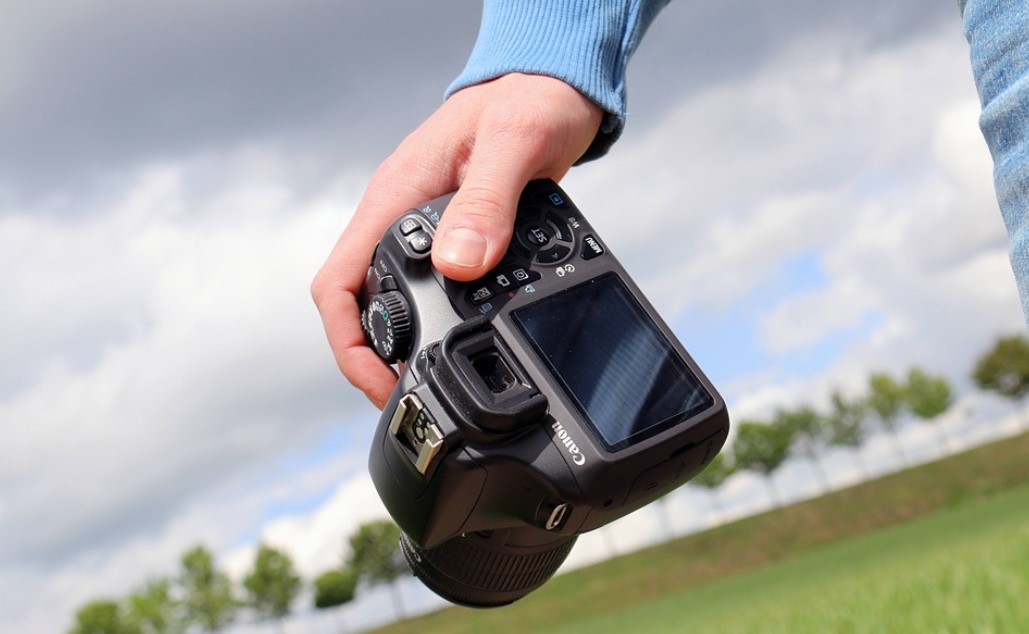