In this blog, we would be introducing the top 5 plastic trends for 2020 and even beyond. If you are dealing in any plastic, or are a business owner for any plastic product, these trends would be highly benefitting for you.
Focus on the sustainability
With the increase in the dangers to the environment and climate change, the issues related to sustainability and its importance have risen to the surface.
That is why most OEMs focus on low volume injection molding because the plant and machinery parts can become more durable, less burdensome, and more useful for realizing the ultimate capacity of the product and the plant.
The entire product lifecycle using these modeling techniques help to reduce the scrap count, utilize the resources more, own the precision and repeatability like none other technology for manufacturing the most useful parts of any plant and machinery.
Lightweight and breaking down the total requirements into parts
Be it vehicles, plants, or machinery–when the focus is on sustainability, more importance is given to letting each part become lightweight in 2020 and beyond.
In fact, for these lightweight injection moulding companies China is becoming one of the powerful nations across the South East Pacific region.
Most of the time, the focus is also on the manufacturing of a single part separately. Either for spare or the main use inside the final plant or machinery.
These parts are also used more for purposes like joints, mesh, scaffolds, and the replacements of the existing parts of a plant.
When these final products are manufactured in parts with the ongoing low volume injection molding technologies, there is an increased importance of mobility, ease of use, and applicability of the same part.
The overall adjustment of a final product becomes easier. Now, if there is a single fault in a product, it can be replaced without having to scrap the entire plant out of the system.
3D printing as a source for prototypes and other experimentations
The 3D printing might not be an exact alternative to the injection molding tactics opted for manufacturers or OEMs. But this trend in the plastic industry is picking up speed for sure. Within 100-500 cycles, 3D printers can manufacture parts that otherwise take a lot of time to get finalized.
These printers often have better printing molds. With the helping of these efficient printing molds, the chances of error decrease drastically. So, moulding companies in China regularly try new experiments and plastic products to be manufactured using 3D printers to save cost, time, and their existing resources.
However, we can say that 3D printing technology is best for creating prototypes. These prototypes are the dummies or the beta versions of the final products or parts. When these prototypes are put into use, researchers or manufacturers know more about the fault that the part or product can render.
After a precise estimation has been made, these manufacturers then make corrections in the measurements on the CAD and then start to finalize the printing of the final product to be launched in the market.
Techniques including automation and industry 4.0
The process of automation in the plastics industry is the way ahead. The processes help to reduce the unwanted cost and large frame of time. Industry 4.0 also includes the use of robotics, mechanical engineering tactics, VR, AR, and so many concepts put together to set a revolution in the market.
The cycles for the low volume injection molding under the automated assembly lines and the industry 4.0 phase of manufacturing are faster, safer, and much more accurate than before.
Robotic initiatives involving axis-joints arms, safety features, servo wrists, and more have a crisp programming and timely backend on the CAD software.
This is all taken into consideration by the Chinese companies whenever they plan to upgrade the quality and quantity of the upcoming manufacturing of prototypes, designs, molds, and other baseline products for an entire industry.
Replacement of metals in cars and other vehicles
It’s noted that by 2025, an average vehicle or automobile would have 5-10 percent of its parts to be plastic. This is in the vision of making every car flexible, safe, and lightweight to drive and use.
The original metal market for automotive parts shifted from rubber, then to the vivid and continual use of plastics injected by injection moulding companies, China.
Related Posts
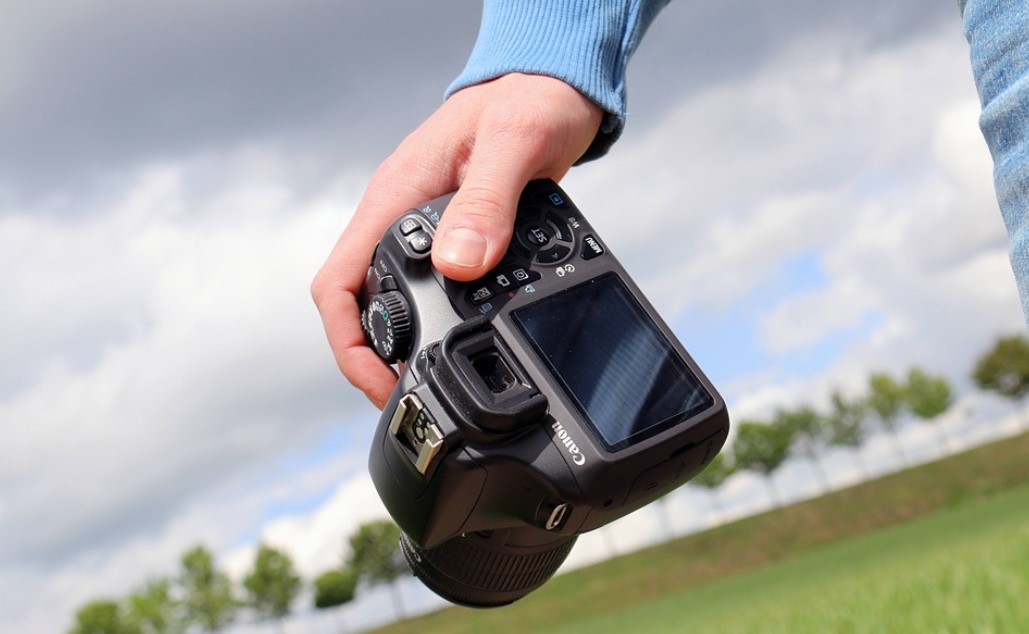